Destylacja rozpuszczalników to proces, który polega na oddzieleniu składników mieszaniny na podstawie różnic w ich temperaturach wrzenia. W praktyce oznacza to, że gdy mieszanina jest podgrzewana, składnik o najniższej temperaturze wrzenia paruje jako pierwszy, a następnie skrapla się w chłodnicy, co pozwala na jego zbieranie w osobnym naczyniu. Proces ten jest szeroko stosowany w chemii oraz przemyśle, gdzie czystość rozpuszczalników ma kluczowe znaczenie dla jakości końcowego produktu. Aby skutecznie przeprowadzić destylację, należy zadbać o odpowiednie warunki, takie jak kontrola temperatury oraz ciśnienia. Warto również zwrócić uwagę na rodzaj używanego sprzętu, ponieważ różne aparaty destylacyjne mogą wpływać na efektywność procesu. W przypadku rozpuszczalników organicznych często stosuje się destylację prostą lub frakcyjną, w zależności od liczby składników oraz ich właściwości fizykochemicznych.
Jakie są zastosowania destylacji rozpuszczalników w przemyśle
Destylacja rozpuszczalników ma wiele zastosowań w różnych gałęziach przemysłu, co czyni ją jednym z najważniejszych procesów technologicznych. W przemyśle chemicznym destylacja jest wykorzystywana do oczyszczania surowców oraz produktów końcowych, co pozwala na uzyskanie wysokiej jakości substancji chemicznych. Na przykład, w produkcji alkoholu etylowego destylacja jest kluczowym etapem, który pozwala na oddzielenie etanolu od innych składników fermentacji. Ponadto w przemyśle farmaceutycznym proces ten jest niezbędny do uzyskiwania czystych rozpuszczalników, które są wykorzystywane w syntezach chemicznych oraz analizach laboratoryjnych. W branży petrochemicznej destylacja frakcyjna służy do separacji różnych frakcji ropy naftowej, co umożliwia produkcję paliw oraz innych produktów naftowych. Również w laboratoriach analitycznych destylacja jest powszechnie stosowana do przygotowywania próbek do dalszych badań.
Jakie są różnice między destylacją prostą a frakcyjną
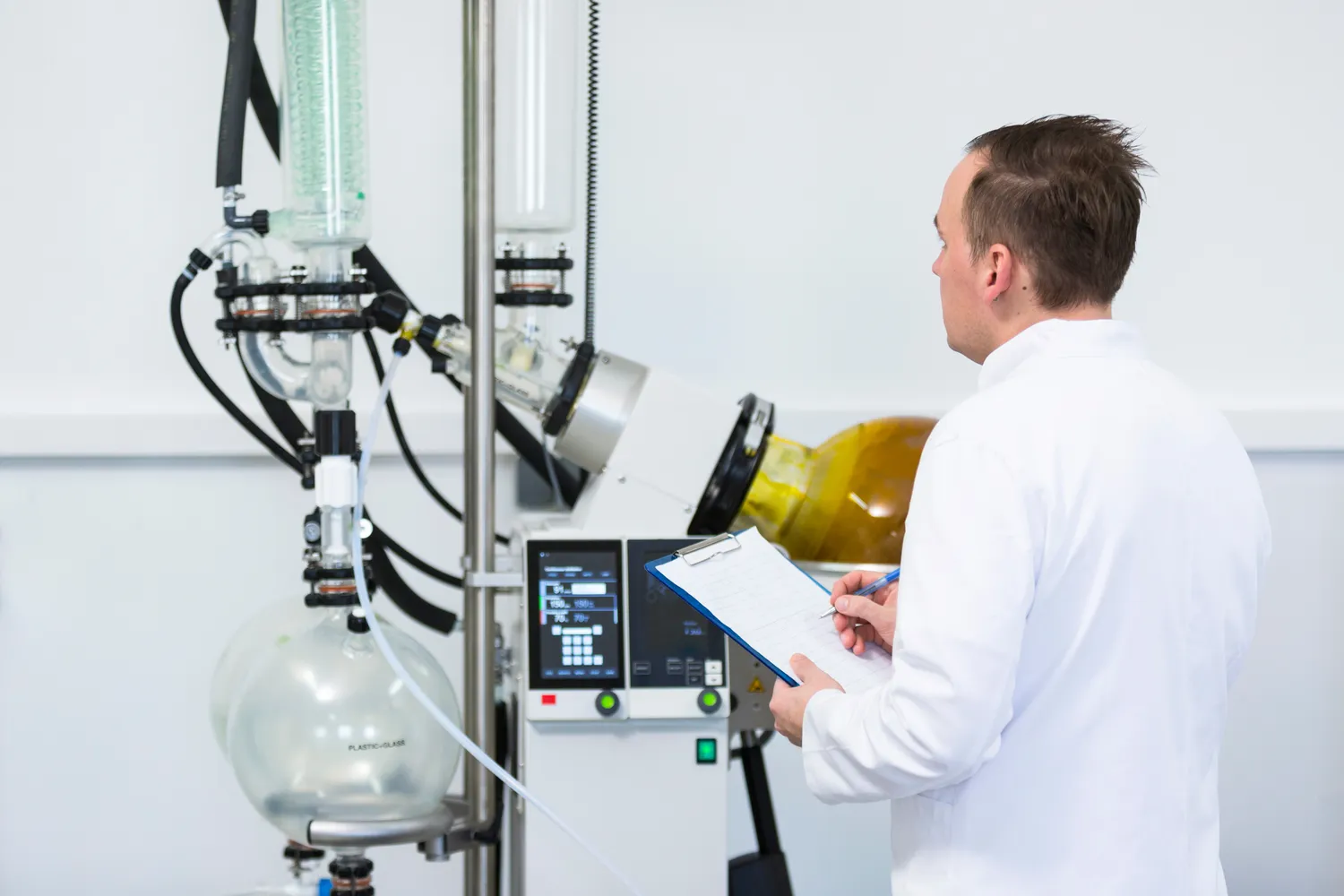
Destylacja prosta i frakcyjna to dwa podstawowe rodzaje procesów destylacyjnych, które różnią się zarówno pod względem zastosowania, jak i efektywności separacji składników. Destylacja prosta jest najczęściej stosowana do oddzielania substancji o znacznie różniących się temperaturach wrzenia, co sprawia, że proces ten jest stosunkowo łatwy i szybki. Przykładem może być oczyszczanie wody z zanieczyszczeń poprzez jej podgrzewanie i skraplanie pary wodnej. Z kolei destylacja frakcyjna jest bardziej skomplikowana i polega na wielokrotnym parowaniu i skraplaniu składników mieszaniny w kolumnie frakcyjnej. Dzięki temu możliwe jest uzyskanie większej czystości poszczególnych frakcji oraz efektywniejsze oddzielanie substancji o zbliżonych temperaturach wrzenia. Proces ten znajduje zastosowanie głównie w przemyśle chemicznym i petrochemicznym, gdzie wymagana jest wysoka jakość produktów końcowych.
Jakie są najczęstsze problemy podczas destylacji rozpuszczalników
Podczas przeprowadzania procesu destylacji rozpuszczalników można napotkać różnorodne problemy, które mogą wpłynąć na efektywność i jakość uzyskiwanych produktów. Jednym z najczęstszych problemów jest nieodpowiednia kontrola temperatury, która może prowadzić do niepełnego oddzielenia składników lub ich niepożądanego mieszania. Zbyt wysoka temperatura może spowodować degradację termiczną niektórych substancji, co negatywnie wpłynie na jakość końcowego produktu. Innym problemem może być niewłaściwe dobranie sprzętu destylacyjnego; użycie kolumny frakcyjnej o niewłaściwej wysokości lub liczbie teoretycznych półek może ograniczyć efektywność separacji. Dodatkowo zjawisko tworzenia się azeotropów może stanowić istotne wyzwanie podczas destylacji niektórych mieszanin; azeotropy to mieszaniny o stałym składzie, które mają tę samą temperaturę wrzenia jak ich składniki, co utrudnia ich dalszą separację.
Jakie są najważniejsze czynniki wpływające na efektywność destylacji
Efektywność procesu destylacji rozpuszczalników zależy od wielu czynników, które mogą znacząco wpłynąć na jakość i ilość uzyskiwanego produktu. Jednym z kluczowych elementów jest temperatura wrzenia składników mieszaniny; im większa różnica w temperaturach wrzenia, tym łatwiejsze jest ich oddzielenie. W przypadku substancji o zbliżonych temperaturach wrzenia, takich jak niektóre rozpuszczalniki organiczne, proces może być znacznie bardziej skomplikowany i wymaga zastosowania destylacji frakcyjnej. Kolejnym istotnym czynnikiem jest ciśnienie atmosferyczne; obniżenie ciśnienia pozwala na obniżenie temperatury wrzenia, co może być korzystne w przypadku substancji wrażliwych na wysoką temperaturę. Również konstrukcja aparatu destylacyjnego ma znaczenie; kolumny frakcyjne z odpowiednią liczbą teoretycznych półek umożliwiają lepszą separację składników. Dodatkowo, czas trwania procesu oraz szybkość podgrzewania również wpływają na efektywność destylacji.
Jakie są nowoczesne technologie stosowane w destylacji rozpuszczalników
W ostatnich latach rozwój technologii przyczynił się do wprowadzenia innowacyjnych rozwiązań w procesie destylacji rozpuszczalników, co pozwala na zwiększenie efektywności oraz oszczędności energetycznych. Jednym z takich rozwiązań jest zastosowanie destylacji membranowej, która wykorzystuje specjalne membrany do separacji składników mieszaniny. Ta metoda charakteryzuje się niższym zużyciem energii oraz mniejszymi stratami materiałowymi w porównaniu do tradycyjnych metod destylacyjnych. Innowacyjne podejście obejmuje także wykorzystanie technologii mikrofalowej, która umożliwia szybsze podgrzewanie cieczy i tym samym przyspiesza proces destylacji. Dodatkowo, automatyzacja procesów destylacyjnych za pomocą systemów sterowania i monitorowania pozwala na precyzyjne zarządzanie warunkami pracy, co zwiększa bezpieczeństwo oraz jakość produktów końcowych. Warto również wspomnieć o zastosowaniu technologii superkrytycznej, która umożliwia separację składników w stanie superkrytycznym, co otwiera nowe możliwości w zakresie oczyszczania i ekstrakcji substancji chemicznych.
Jakie są różnice między destylacją a innymi metodami separacji
Destylacja jest jedną z wielu metod separacji składników mieszanin chemicznych, ale różni się od innych technik zarówno pod względem zasady działania, jak i zastosowań. Na przykład, filtracja to metoda mechaniczna polegająca na oddzieleniu ciał stałych od cieczy za pomocą materiału filtracyjnego. Filtracja jest skuteczna w przypadku zawiesin, ale nie nadaje się do separacji cieczy o podobnych właściwościach fizykochemicznych. Z kolei ekstrakcja to proces, który polega na przenoszeniu składnika z jednej fazy do drugiej, często przy użyciu rozpuszczalnika. Ekstrakcja może być bardziej selektywna niż destylacja, ale wymaga odpowiedniego doboru rozpuszczalnika oraz warunków reakcji. Inne metody separacji to chromatografia, która wykorzystuje różnice w adsorpcji składników na powierzchni materiału stacjonarnego; ta technika jest szczególnie przydatna w analizach chemicznych oraz oczyszczaniu substancji o wysokiej czystości.
Jakie są aspekty ekologiczne związane z procesem destylacji
W kontekście rosnącej świadomości ekologicznej i potrzeby ochrony środowiska aspekty ekologiczne związane z procesem destylacji stają się coraz bardziej istotne. Proces ten często wiąże się z dużym zużyciem energii, zwłaszcza gdy wymagana jest wysoka temperatura do przeprowadzenia destylacji. Dlatego poszukiwanie bardziej energooszczędnych metod staje się priorytetem dla wielu przedsiębiorstw chemicznych. Wprowadzenie technologii takich jak destylacja membranowa czy mikrofalowa może przyczynić się do zmniejszenia zużycia energii oraz emisji gazów cieplarnianych związanych z procesami przemysłowymi. Ponadto ważne jest również zarządzanie odpadami powstającymi podczas destylacji; odpady te mogą zawierać niebezpieczne substancje chemiczne, które wymagają odpowiedniego traktowania i utylizacji zgodnie z przepisami ochrony środowiska.
Jakie są przyszłe kierunki badań nad destylacją rozpuszczalników
Przyszłość badań nad destylacją rozpuszczalników wydaje się obiecująca dzięki ciągłemu postępowi technologicznemu oraz rosnącym wymaganiom dotyczącym efektywności i ekologiczności procesów przemysłowych. Wśród najważniejszych kierunków badań można wymienić rozwój nowych materiałów dla kolumn frakcyjnych oraz membran stosowanych w nowoczesnych technologiach separacyjnych. Badania te mają na celu zwiększenie efektywności separacji oraz obniżenie kosztów operacyjnych związanych z procesem destylacji. Również eksploracja zastosowania sztucznej inteligencji i uczenia maszynowego w optymalizacji parametrów procesu staje się coraz bardziej popularna; takie podejście może prowadzić do lepszego zarządzania warunkami pracy oraz przewidywania potencjalnych problemów podczas destylacji. Dodatkowo badania nad alternatywnymi źródłami energii dla procesów chemicznych mogą przyczynić się do zwiększenia zrównoważonego rozwoju branży chemicznej poprzez zmniejszenie jej śladu węglowego.
Jakie są kluczowe wyzwania w przemyśle związanym z destylacją
W przemyśle chemicznym związanym z destylacją rozpuszczalników istnieje wiele kluczowych wyzwań, które mogą wpłynąć na efektywność i bezpieczeństwo procesów produkcyjnych. Jednym z głównych problemów jest konieczność ciągłego dostosowywania się do zmieniających się regulacji dotyczących ochrony środowiska oraz bezpieczeństwa pracy. Firmy muszą inwestować w nowoczesne technologie, które spełniają te wymagania, co często wiąże się z wysokimi kosztami. Dodatkowo, zarządzanie jakością surowców oraz produktów końcowych stanowi istotne wyzwanie; niejednorodność materiałów może prowadzić do problemów podczas destylacji, wpływając na czystość uzyskiwanych substancji. Wreszcie, zmiany w popycie na różne rozpuszczalniki oraz ich zastosowania mogą wymusić na przedsiębiorstwach elastyczność w produkcji i dostosowywaniu procesów technologicznych.