Destylator przemysłowy to urządzenie, które odgrywa kluczową rolę w wielu procesach produkcyjnych, szczególnie w przemyśle chemicznym i petrochemicznym. Jego głównym zadaniem jest separacja składników mieszanin ciekłych na podstawie różnic w ich temperaturze wrzenia. Proces destylacji polega na podgrzewaniu cieczy do momentu, gdy zaczyna parować, a następnie schładzaniu pary, aby skondensować ją z powrotem do stanu ciekłego. W przemyśle stosuje się różne rodzaje destylatorów, w tym destylatory prostokątne, kolumnowe oraz frakcyjne, które są dostosowane do specyficznych potrzeb produkcji. W przypadku destylacji frakcyjnej, która jest najczęściej stosowana w przemyśle naftowym, wykorzystuje się kolumny o dużej wysokości, w których zachodzi wielokrotna kondensacja i parowanie. Dzięki temu możliwe jest uzyskanie wysokiej czystości produktów końcowych. Destylatory przemysłowe są również wykorzystywane do produkcji alkoholu, gdzie kluczowym etapem jest oddzielenie etanolu od innych składników fermentacji.
Jakie są zastosowania destylatorów przemysłowych w różnych branżach
Destylatory przemysłowe znajdują szerokie zastosowanie w różnych branżach, co czyni je niezwykle wszechstronnymi urządzeniami. W przemyśle chemicznym służą do separacji i oczyszczania substancji chemicznych, co jest niezbędne dla uzyskania wysokiej jakości produktów. Na przykład w produkcji kwasu siarkowego czy amoniaku procesy destylacyjne są kluczowe dla efektywności produkcji. W przemyśle naftowym destylatory są wykorzystywane do rafinacji ropy naftowej, gdzie oddziela się różne frakcje paliwowe takie jak benzyna, olej napędowy czy olej opałowy. W branży spożywczej destylatory przemysłowe są używane do produkcji napojów alkoholowych, takich jak whisky czy wódka, gdzie istotne jest uzyskanie odpowiedniej jakości trunku poprzez precyzyjne oddzielenie etanolu od innych substancji. Ponadto w przemyśle farmaceutycznym destylacja jest kluczowym procesem przy produkcji leków i substancji czynnych.
Jakie są najważniejsze elementy budowy destylatora przemysłowego
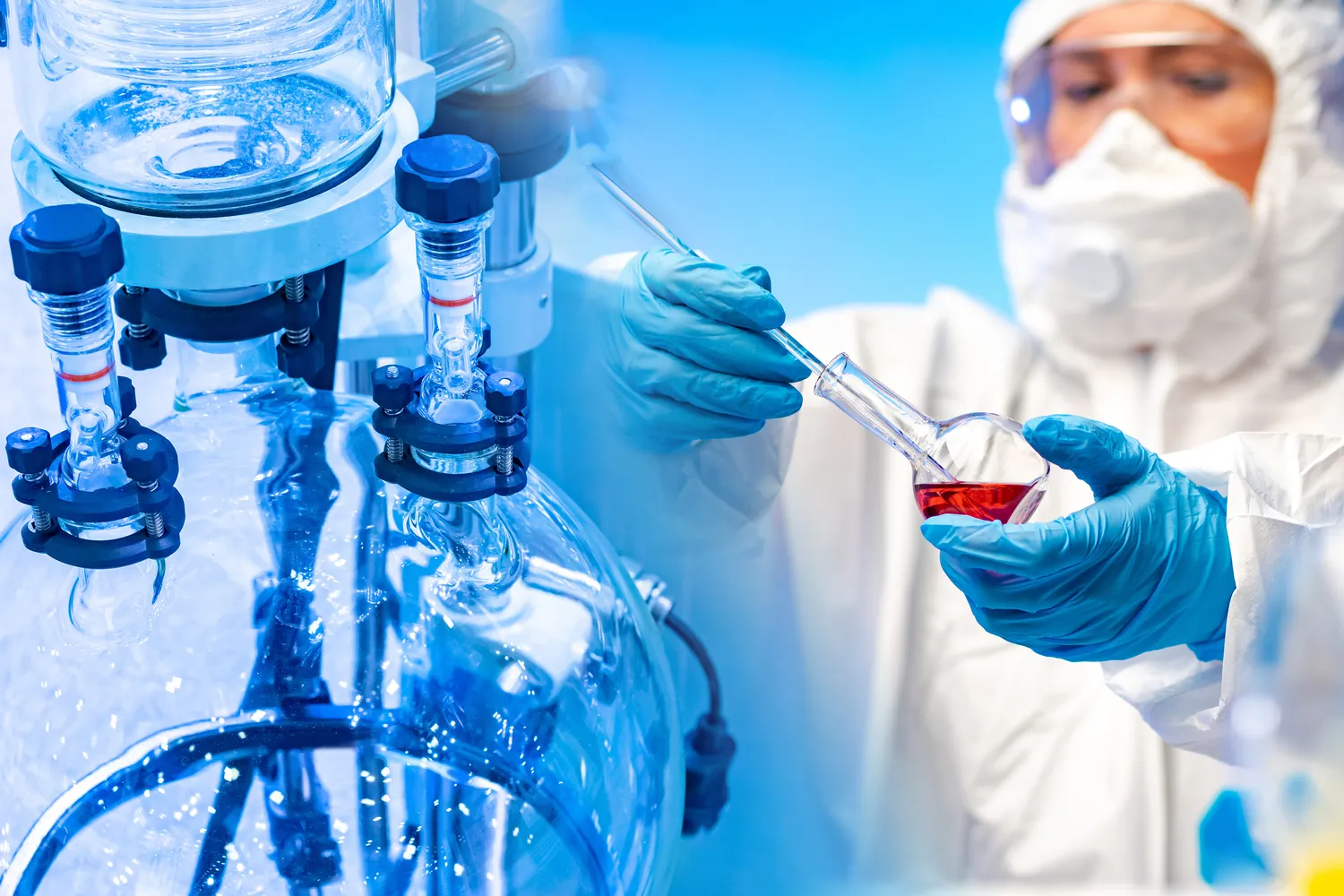
Budowa destylatora przemysłowego opiera się na kilku kluczowych elementach, które współdziałają ze sobą w celu efektywnego przeprowadzenia procesu destylacji. Podstawowym elementem jest zbiornik, w którym umieszczana jest mieszanina cieczy do destylacji. Zbiornik ten jest zazwyczaj wyposażony w system grzewczy, który podgrzewa ciecz do odpowiedniej temperatury wrzenia. Kolejnym istotnym elementem jest kolumna destylacyjna, która może mieć różną wysokość i średnicę w zależności od wymagań procesu. Kolumna ta zawiera tzw. „wypełnienie”, które zwiększa powierzchnię kontaktu między parą a cieczą, co sprzyja efektywniejszej separacji składników. Na szczycie kolumny znajduje się skraplacz, który schładza parę i kondensuje ją z powrotem do stanu ciekłego. Oprócz tych podstawowych komponentów, nowoczesne destylatory często wyposażone są w systemy automatyzacji i monitorowania parametrów procesu, co pozwala na lepszą kontrolę nad jakością produktów końcowych oraz zwiększa bezpieczeństwo operacji.
Jakie są zalety stosowania nowoczesnych destylatorów przemysłowych
Nowoczesne destylatory przemysłowe oferują szereg zalet, które przyczyniają się do poprawy efektywności procesów produkcyjnych oraz jakości uzyskiwanych produktów. Jedną z głównych korzyści jest zwiększona wydajność energetyczna dzięki zastosowaniu zaawansowanych technologii grzewczych oraz izolacyjnych. Dzięki temu możliwe jest zredukowanie kosztów operacyjnych związanych z zużyciem energii. Kolejną zaletą nowoczesnych destylatorów jest ich zdolność do pracy z różnorodnymi mieszaninami cieczy oraz możliwość dostosowania parametrów pracy do specyficznych wymagań danego procesu. Automatyzacja i systemy monitorowania pozwalają na bieżące śledzenie parametrów procesu oraz szybką reakcję na ewentualne nieprawidłowości, co zwiększa bezpieczeństwo operacji i minimalizuje ryzyko awarii. Nowoczesne technologie umożliwiają również osiągnięcie wyższej czystości produktów końcowych poprzez bardziej precyzyjne sterowanie procesem separacji składników.
Jakie są najczęstsze problemy związane z destylatorami przemysłowymi
Destylatory przemysłowe, mimo swojej zaawansowanej technologii, mogą napotykać różne problemy, które wpływają na efektywność ich działania. Jednym z najczęstszych problemów jest zatykanie kolumny destylacyjnej, co może być spowodowane osadzaniem się zanieczyszczeń lub nieodpowiednim wypełnieniem. Zatykanie kolumny prowadzi do obniżenia wydajności procesu oraz zwiększenia zużycia energii. Innym istotnym problemem jest niestabilność temperatury w zbiorniku lub kolumnie, co może prowadzić do nieefektywnej separacji składników. Wahania temperatury mogą być spowodowane niewłaściwym działaniem systemu grzewczego lub błędami w automatyzacji procesu. Dodatkowo, niewłaściwe ustawienia parametrów pracy, takich jak ciśnienie czy przepływ cieczy, mogą prowadzić do obniżenia jakości produktów końcowych. Problemy te mogą również skutkować zwiększeniem kosztów produkcji oraz wydłużeniem czasu realizacji procesów.
Jakie są różnice między destylatorami przemysłowymi a laboratoryjnymi
Destylatory przemysłowe i laboratoryjne różnią się pod wieloma względami, co wynika z ich przeznaczenia oraz skali działania. Destylatory przemysłowe są zazwyczaj znacznie większe i bardziej skomplikowane niż ich laboratoryjne odpowiedniki. Ich konstrukcja jest dostosowana do pracy w warunkach ciągłej produkcji, co oznacza, że muszą być w stanie obsługiwać duże ilości surowców i produktów końcowych. W przeciwieństwie do tego destylatory laboratoryjne są zazwyczaj mniejsze i bardziej elastyczne, co pozwala na przeprowadzanie eksperymentów oraz testów w kontrolowanych warunkach. Kolejną różnicą jest stopień automatyzacji; destylatory przemysłowe często wyposażone są w zaawansowane systemy monitorowania i automatyzacji, które umożliwiają precyzyjne sterowanie procesem oraz zbieranie danych na temat jego przebiegu. W laboratoriach natomiast często korzysta się z manualnych metod obsługi, co pozwala na większą kontrolę nad poszczególnymi etapami destylacji. Ponadto destylatory przemysłowe muszą spełniać rygorystyczne normy bezpieczeństwa oraz ochrony środowiska, co wpływa na ich konstrukcję i materiały użyte do produkcji.
Jakie są koszty eksploatacji destylatorów przemysłowych
Koszty eksploatacji destylatorów przemysłowych mogą być znaczące i zależą od wielu czynników, takich jak rodzaj stosowanego surowca, skala produkcji oraz technologie wykorzystywane w procesie destylacji. Jednym z głównych składników kosztów jest energia potrzebna do podgrzewania cieczy w zbiorniku oraz utrzymania odpowiedniej temperatury w kolumnie destylacyjnej. W przypadku dużych instalacji przemysłowych koszty energii mogą stanowić znaczną część całkowitych wydatków operacyjnych. Dodatkowo należy uwzględnić koszty związane z konserwacją i serwisowaniem urządzeń, które są niezbędne dla zapewnienia ich prawidłowego działania oraz minimalizacji ryzyka awarii. Koszty te mogą obejmować zarówno regularne przeglądy techniczne, jak i wymianę części eksploatacyjnych. Warto również pamiętać o kosztach związanych z przestrzeganiem norm bezpieczeństwa i ochrony środowiska, które mogą wiązać się z koniecznością inwestycji w dodatkowe systemy filtracyjne czy monitorujące emisje.
Jakie innowacje technologiczne wpływają na rozwój destylatorów przemysłowych
Innowacje technologiczne mają kluczowe znaczenie dla rozwoju destylatorów przemysłowych, przyczyniając się do poprawy efektywności procesów oraz jakości uzyskiwanych produktów. Jednym z najważniejszych trendów jest automatyzacja procesów destylacyjnych, która pozwala na precyzyjne sterowanie parametrami pracy urządzeń oraz bieżące monitorowanie ich stanu. Dzięki nowoczesnym systemom informatycznym możliwe jest zbieranie danych o przebiegu procesu w czasie rzeczywistym, co umożliwia szybką reakcję na ewentualne nieprawidłowości. Kolejnym istotnym kierunkiem rozwoju jest zastosowanie nowych materiałów budowlanych i technologii izolacyjnych, które pozwalają na zwiększenie efektywności energetycznej destylatorów oraz redukcję strat ciepła. Innowacje te przyczyniają się do obniżenia kosztów eksploatacji oraz zmniejszenia wpływu na środowisko naturalne. Ponadto rozwój technologii membranowych oraz alternatywnych metod separacji składników otwiera nowe możliwości dla procesów destylacyjnych, umożliwiając uzyskiwanie wyższej czystości produktów końcowych przy mniejszym zużyciu energii.
Jakie są przyszłościowe kierunki rozwoju technologii destylacyjnej
Przyszłość technologii destylacyjnej wydaje się obiecująca dzięki ciągłemu rozwojowi innowacji oraz rosnącemu zapotrzebowaniu na wysokiej jakości produkty chemiczne i spożywcze. Jednym z kluczowych kierunków rozwoju jest dalsza automatyzacja procesów produkcyjnych, która pozwoli na jeszcze większą precyzję w zarządzaniu parametrami pracy destylatorów oraz optymalizację wydajności energetycznej. W miarę jak technologia sztucznej inteligencji staje się coraz bardziej powszechna, można spodziewać się zastosowania algorytmów uczenia maszynowego do analizy danych procesowych i przewidywania potencjalnych problemów przed ich wystąpieniem. Kolejnym istotnym trendem jest rozwój technologii ekologicznych, które mają na celu minimalizację wpływu procesów przemysłowych na środowisko naturalne poprzez redukcję emisji gazów cieplarnianych oraz odpadowych produktów ubocznych. Technologie takie jak odzysk ciepła czy zastosowanie odnawialnych źródeł energii będą miały kluczowe znaczenie dla przyszłości branży destylacyjnej.